Engineering the 1470 Hillside Combine
By Don Murray, leader of the IH Axial-Flow project
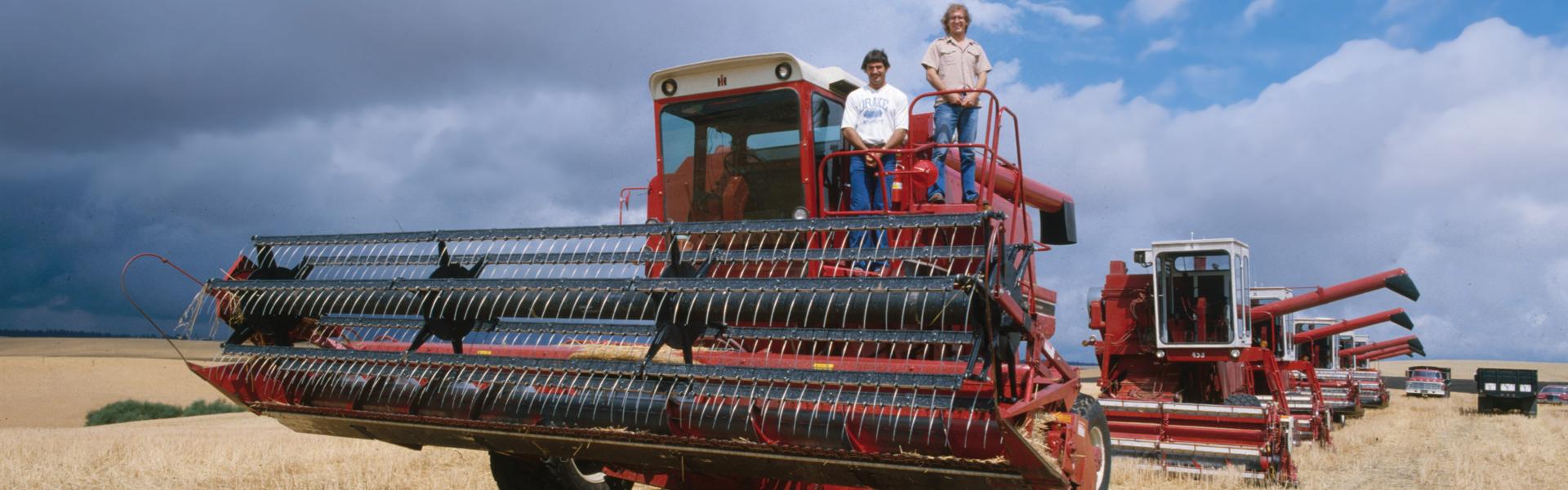
The following is an excerpt from the diary of Don Murray, IH chief engineer for Grain Harvesting Engineering. Murray was the leader of the Axial-Flow project and kept a detailed written account of the process, providing an insider’s view of the trials and tribulations faced during the development of the Axial-Flow combine. In this chapter, Murray chronicles the development of the 1470 hillside combine, from boardroom conception and preproduction testing all the way up to performance out on the field and in salesrooms.
Find more development narratives of Don Murray’s in Red Combines 1915–2015, including the CX-1, CX-14, and CX-18 prototypes that led to the creation of the original Axial-Flow combine.
------------------------------
THE 1470 HILLSIDE COMBINE—SETTING A NEW STANDARD FOR SIZE AND EXCELLENCE
The hillside program really deserves a chapter of it's own but probably Rich McMillen, Leroy Picket, Norm Stroup and Jim Lucas should write it. However we shall proceed. Pickett was assigned to work on the basic combine configuration, working for Rich as Product Engineer in charge, Stroup to work on the rather extensive hydraulics involved, and Lucas to be responsible for Test and Development to assure product integrity. Today all that is easy to say, but at the time it took considerable investigation and several decisions.
Scanning the Market
We had the 453, an upgrading of the old 403 HS, which we were selling in four-way leveling only. The 453 side-leveled to 32% either right or left, leveled upslope to 32% and downslope to 11%.
Deere had the 6602 hillside version of the 6600 which was probably 15% larger than the 453 and Allis Chalmers made the MH Hillside, about the same size as the IH. Both these were made in two-way (side) leveling only. The 6602 leveled to 45% sideslope. The four-way leveling had real advantages, particularly in the steeper terrain. It not only saved more grain when going up or down hill, it enabled the 453 to put more weight on the front drive wheels, thus giving it a better climbing ability than the JO or AC. So we were getting a higher percentage of the really steep hillside areas while AC & Deere were probably getting a higher portion of the less steep terrain areas.
In 1974 Deere introduced the Sidehill 6600, designed to be a general-purpose combine in those areas that had side slopes of 20% or less and grew a variety of crops, including corn. In short, it was aimed at the Midwest Corn Belt. Of course the Sidehill 6600 was quite a bit more expensive than the standard version but they did find quite a market in the more rolling areas of the corn belt. It was never expanded beyond the one model.
Our Chance to Step In
We had one of those rare opportunities where we were starting out with a clean sheet of paper. I proposed that we should simultaneously develop a sidehill and a hillside version of the Axial-Flow with significant common designs and parts, and was even so bold as to present it in a Divisional Product Review Meeting. When the realistic engineers, particularly Leroy Pickett finished a study of the requirements of the two machines it was obvious Murray had been smoking something—there really was no commonalty if we were to produce a top-notch machine in both categories. We calmed down and concentrated on a good hillside machine for the Pacific Northwest Hillside Country. Sizing the machine was not much of a problem; we didn't have the smaller 20-inch rotor machine far enough along to be a possibility and besides, it would be just a bit smaller than competition, something we could never allow. So it had to be the 1460 size machine.
1470 in field with CX40 header, 1983. Don Murray
1470 in pea field, Washington 1983. Don Murray
Two-Way vs. Four-Way Leveling
One very real problem in laying out the new machine was the two-way vs four-way leveling argument (maybe our sheet of paper was not so clean after all). We had certain trade areas that depended on the IH four-way leveling machine, and the competition just couldn't get up the steepest hills. We were convinced we could save grain up those steep hills without leveling fore and aft, but we had to get up them. Of course, we intended that only hydrostatic propulsion was suitable, so it naturally evolved (hindsight) that if we could hydraulically drive the rear wheels we could get up those steep hills. This would avoid the cost and "spindleness" of the four-way leveling (I am not sure which would cost the most, four-way leveling or four-wheel drive) so it was agreed all machines would have four-wheel drive. Design criteria were set up, and layout work was started to meet that demand. The criteria included sideslope leveling of 44-49%, the theoretical hill climbing ability was 36%, and the forward tipping slope with full grain tank was 70%. The design actually achieved a sideslope leveling capability of 48%.
Looking for Business Partners in the Northwest
We soon realized that the really large machine that would evolve from our criteria was going to be almost impossible to transport from East Moline to the primary trade area, the Pacific Northwest. So we began looking for someone out in Washington, Oregon, or Idaho that could take a standard 1460 and convert it to a hillside machine. I, among others, traveled extensively in the area, looking for a suitable manufacturer. The most favorable seemed to be Love Company at Garfield, Washington. John Love was primarily involved in the Love pickup reel and the flexible floating cutter bar, both sold nationally. His company also made a bean pickup unit sold locally and some rather mundane rod weeders etc. Moreover he was interested. However we were worried, it looked like we might be shoving an elephant at him that his organization just couldn't handle.
At about this time, somebody, and I sure don't remember who, suggested RAHCO at Spokane. We investigated RAHCO and found them to be a very interesting organization. The name came from no other than Raymond A. Hanson, the inventor of the self-leveling control system. The RAHCO organization, managed by Raymond's three sons was expert in slip-form concrete laying equipment, used primarily in large irrigation canals and pipelines then being built throughout the world. They had bought an old WW-2 aluminum or magnesium producing plant just outside of Spokane, which had become their worldwide operations center. Raymond was semi-retired, spending most of his time sort of playing while still keeping a hand on the boys.
Of course, before IH could seriously discuss a possible joint venture with RAHCO, our legal and business people had to investigate the most intimate details of their financial operations, but eventually all agreed we could consider doing business with these Northwestern mavericks. At the time, they were busy working on one option for hiding and activating the nuclear bomb equipped MX missile. Their proposal was to dig a series of very big trenches in a large area of the Southwest, pouring big, like 15 feet diameter concrete tubes in the trenches, and backfilling the trenches. Then the MX missiles would be randomly located on tracks in the tubes, only the military would know where, thus supposedly immune from enemy atomic attack. At the appropriate time, the MX carrier would use its powerful hydraulic system to burst through the tube and the earth so the MX could blast upward to retaliate. Fantastic and futuristic? They were actually building a system and testing it right in their backyard. We understood it was later shipped somewhere to the Southwest desert, and that a short sample section installed but then mothballed behind a steel fence. I wonder if it is still there.
1470 in Washinton, in pea fields. Don Murray
Wisconsin Historical Society
Development Concerns
The concern we immediately saw was that most of their production was one or two of a kind, they didn't worry about mass production, parts interchangeability, and all those things that were vital to us. However they had a good engineering department, and such important things as an established purchasing agent and a good accounting system, and they certainly had the manufacturing space in those big old aluminum production buildings. With all this, we finally signed what we thought was to be a "turn key" deal with them—they would receive a special built 1460 and engineer and build and assemble all the parts necessary to complete the hillside machine.
They hired a project manager, one Guy Swanson who was an Agricultural Engineer with considerable experience in the hillside country. Unfortunately, Guy had little experience in manufacturing and was treated as sort of an outcast by both the RAHCO and the IH people. There were times when I didn't envy him his job. We had set up the criteria, had lots of specifics in the contract, and expected things would go smoothly. But that was not to be the case. Pickett worked with them regularly during their engineering phase, sometimes spending two or three weeks at a time up there. The more he worked with them, the more discouraged he became. They just couldn't seem to get away from their "build it extra stout and don't worry about the cost" theory. I found I was up there several times to try to negotiate a peace between IH requirements and RAHCO objectives. When RAHCO people thanked me for my decisions I knew Leroy was not going to be happy, and visa-versa.
Preproduction Tests
Our test department rightly insisted the test machine be checked for structural weakness.
One trip while I was up there, Jim Lucas was applying stress-coat (brittle lacquer some called it) to a large number of areas he by judgment deemed might be critical. Conditions there were not favorable to stress-coat, but as I remember it he had a new formula that could be applied and cured at ambient temperatures. Then they took the machine out on representative hillside applications, brought it back and analyzed the stress crackage patterns—a standard procedure for them but Greek to the rest of us.
In 1979 we had RAHCO build five preproduction machines, which we and marketing placed throughout the hillside area (placed, not sold). Four of them remained in the Northwest, but the fifth, at marketing's insistence, had to go down to Paso Robles, California. There was a small pocket of hillside market down there, not really appropriate for one of the five. The machine had to be partially disassembled and then shipped as a special wide-load truck shipment. Because it was so far from the rest of the activity, it never got good service and was a detriment to the sales area.
Sometimes we are slow to learn, or maybe reluctant to vigorously resist sales "demands," particularly those made by the big California dealers.
Announcing the Model
For some reason that now escapes me (and seems a year premature} on June 19, 1979, we had a big product announcement at the convention center at Spokane introducing the 1470 Hillside Combine to IH marketing people and dealers. We had a machine there, a big slide introduction to the dealers, and I specifically remember Tom St John got stuck with announcing the list price—$115,000 (later increased to $121,688)—far and away the highest price ever asked for a combine (by comparison the 1460 Corn Special with six row corn head was $90,000 and the 453 in 1976 was $50,782, 1977 dollars). There was a gasp from the dealers but by the time the day was over they were reasonably receptive. In D & T 310, 10-20-76 we had projected a list price of $68,423 (1977 dollars) for a two-way leveling, two-wheel drive 1460 Axial-Flow Hillside Combine. Obviously, we had raised our sights—and our costs—considerably.
Power to the 1470 was supplied by a 210-hp DT466 engine. The 1470 was based on the 1460 and used the 24-inch rotor from the 1460 and a 145-bushel grain tank. The four-way leveling machine could handle slopes with a grande of up to 48 percent. Wisconsin Historical Society #114884
1470, custom cutter machines, in Lind, Washington, 1980. Don Murray
Much-Needed Improvements
By August of 1979, quite a number of machine areas had surfaced that demanded improvement. Also, the marginal "producibility-reliability" of the RAHCO drawings was becoming evident. We had both Leroy Pickett and Rich McMillen, along with three or four other of our own Product and Test Engineers up there working on solutions. In addition we had three or four engineers back at East Moline working on the design and drawings.
Leroy wanted to bring all the drawings back to East Moline and have our own engineers go over the whole design and upgrade the drawings to our standards. I did not agree with this, not that it was not the best program for the hillside but that it would have been a major disruption to all the rest of our programs. Rich finally worked out a compromise where East Moline Engineers went over a lot of the really critical areas and worked with RAHCO engineers on the rest of the design. Right in the middle of this, Gene Krukow, Norm Stroup and Dick Staiert were having a field day with all the real "gut issues": the hydraulics and electronics involved. They worked well with the rest of the group and the challenge of this project was what they had dreamed of for years. In many ways the ultimate success of the program was due to their aggressive understanding and solution of complex hydraulic, hydrostatic propulsion and electronic control challenges, together with Leroy Pickett's dogged determination to have a machine that was right and Jim Lucas' continual evaluation of the product to see that it was right. It was an excellent team effort.
Into Production
By early 1980, IH and RAHCO worked out the problems both in design and with the contract, and went into production. Considering the tremendous internal problems that had to be resolved, the resulting product was a very good professional representation, a product both IH and RAHCO were proud of. What had started out to be a "turn key" product where RAHCO was to do all the "hill siding" had gradually evolved into IH both paying RAHCO for their engineering effort and investing considerable of our own engineering manpower. The project ended up costing our engineering department just over $1,000,000: double our original estimate. But, very important, IH got the manufacture and distribution problems resolved. We also got into production one year earlier than our 1976 projections (1980 vs. 1981).
We never did go back and try to develop a "sidehill" version of the Axial-Flow to match the JO Sidehill 6600. Deere Sidehill 6600 sales were never spectacular, but they did justify the one model. In 1976 they sold 654 units (Macmillen and Harrington, John Deere Tractors and Equipment, Vol. 2) which is estimated at a little over 10% of their 6600 sales. If we had proceeded, it is doubtful if we could have gained much net sales. Incidentally, as I understand it Deere later went to RAHCO to have them produce the next generation JD hillside model. By that time, I was retired and not worrying about who owned tooling, engineering and all the ramifications. As far as I know the arrangement is still in effect.
Pickett, Stroup and Lucas presented a paper at the 1980 Winter Meeting, American Society of Agricultural Engineers 5, and later in October 1981, Norm Stroup and Gene Krukow presented a paper describing the hydraulic system at the National Conference on Fluid Power. IH Combine Engineers were again showing the professional societies that they were pushing the frontier in engineering farm machinery.
Production Figures
We here only have production figures for 1980 and 81. There are two or three sources of figures, which for a change do agree. It appears that in 1980 we shipped 130 machines to RAHCO for conversion and in 1981 we sent 170 units out to Spokane or 300 in the two years (plus the five reconditioned pre-production machines). Another chart shows retail sales of 102 in 1980, 145 in 81 with inventory of 58 at end of 81 or 305 total accounted for. The annual total market for hillside combines at that time was probably 300–500 machines (in 1976 Deere sold about 260 6602 machines, probably their best year). We had been selling 130-160 of the 453's in the mid and late seventies. Of course one irony was that in presenting a substantially larger combine we were cutting the market potential in unit volume.
Production figures provided by Don Murray
Production figures provided by Don Murray
At a retirement celebration at East Moline in June, 1982, Bev and I were presented with a beautiful framed photograph of four 1470 combines harvesting double windrows of Kentucky Blue Grass just Southeast of Spokane. On the back is an explanation. "A family of four brothers owned eight John Deere's. They traded them in for four IH combines. It is well known that one 1470 will do the work of two John Deere's," -- Camiel Beert.
This whole hillside endeavor is a typical example of IH efforts to fill the "niche markets" to obtain overall coverage throughout the country and to provide local IH dealers in each area a full line of products for their area needs.
Find more engineering and development narratives from Don Murray's experience leading the Axial-Flow combine project in Red Combines 1915–2015.
Find more development narratives of Don Murray’s in Red Combines 1915–2015, including the CX-1, CX-14, and CX-18 prototypes that led to the creation of the original Axial-Flow combine.
------------------------------
THE 1470 HILLSIDE COMBINE—SETTING A NEW STANDARD FOR SIZE AND EXCELLENCE
The hillside program really deserves a chapter of it's own but probably Rich McMillen, Leroy Picket, Norm Stroup and Jim Lucas should write it. However we shall proceed. Pickett was assigned to work on the basic combine configuration, working for Rich as Product Engineer in charge, Stroup to work on the rather extensive hydraulics involved, and Lucas to be responsible for Test and Development to assure product integrity. Today all that is easy to say, but at the time it took considerable investigation and several decisions.
Scanning the Market
We had the 453, an upgrading of the old 403 HS, which we were selling in four-way leveling only. The 453 side-leveled to 32% either right or left, leveled upslope to 32% and downslope to 11%.
Deere had the 6602 hillside version of the 6600 which was probably 15% larger than the 453 and Allis Chalmers made the MH Hillside, about the same size as the IH. Both these were made in two-way (side) leveling only. The 6602 leveled to 45% sideslope. The four-way leveling had real advantages, particularly in the steeper terrain. It not only saved more grain when going up or down hill, it enabled the 453 to put more weight on the front drive wheels, thus giving it a better climbing ability than the JO or AC. So we were getting a higher percentage of the really steep hillside areas while AC & Deere were probably getting a higher portion of the less steep terrain areas.
In 1974 Deere introduced the Sidehill 6600, designed to be a general-purpose combine in those areas that had side slopes of 20% or less and grew a variety of crops, including corn. In short, it was aimed at the Midwest Corn Belt. Of course the Sidehill 6600 was quite a bit more expensive than the standard version but they did find quite a market in the more rolling areas of the corn belt. It was never expanded beyond the one model.
Our Chance to Step In
We had one of those rare opportunities where we were starting out with a clean sheet of paper. I proposed that we should simultaneously develop a sidehill and a hillside version of the Axial-Flow with significant common designs and parts, and was even so bold as to present it in a Divisional Product Review Meeting. When the realistic engineers, particularly Leroy Pickett finished a study of the requirements of the two machines it was obvious Murray had been smoking something—there really was no commonalty if we were to produce a top-notch machine in both categories. We calmed down and concentrated on a good hillside machine for the Pacific Northwest Hillside Country. Sizing the machine was not much of a problem; we didn't have the smaller 20-inch rotor machine far enough along to be a possibility and besides, it would be just a bit smaller than competition, something we could never allow. So it had to be the 1460 size machine.
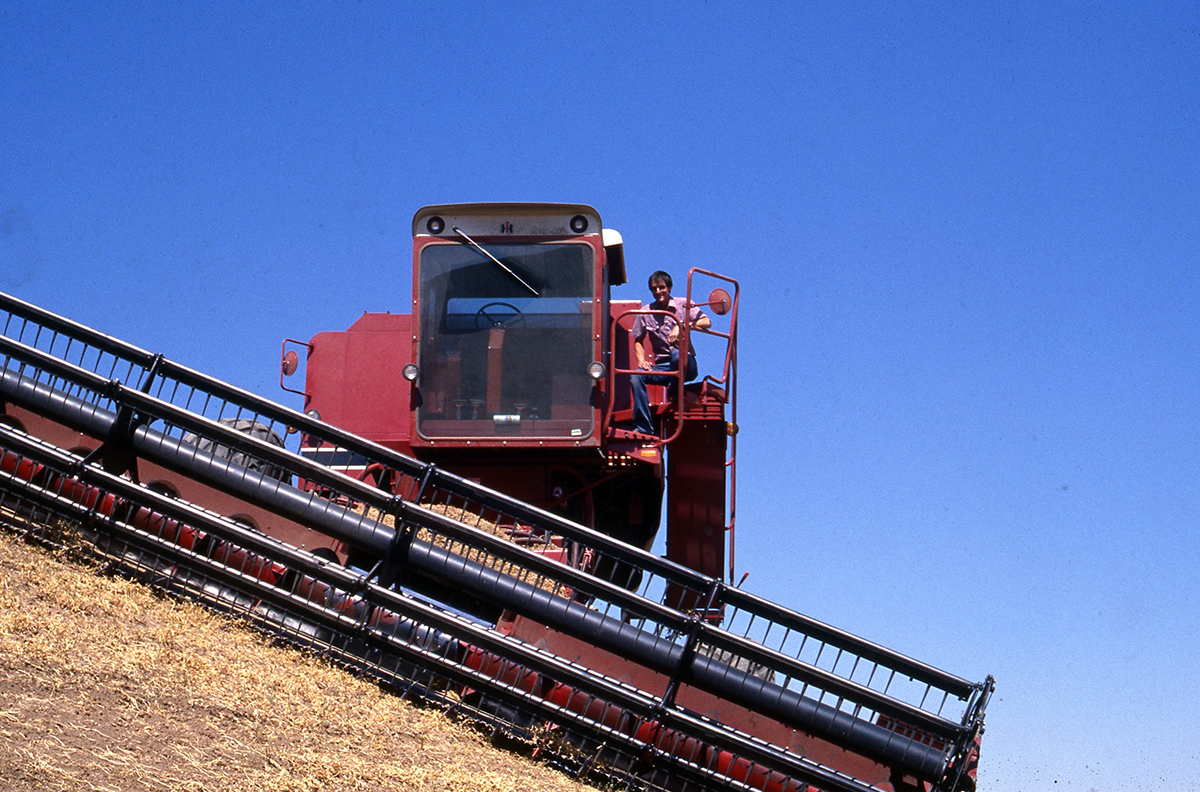
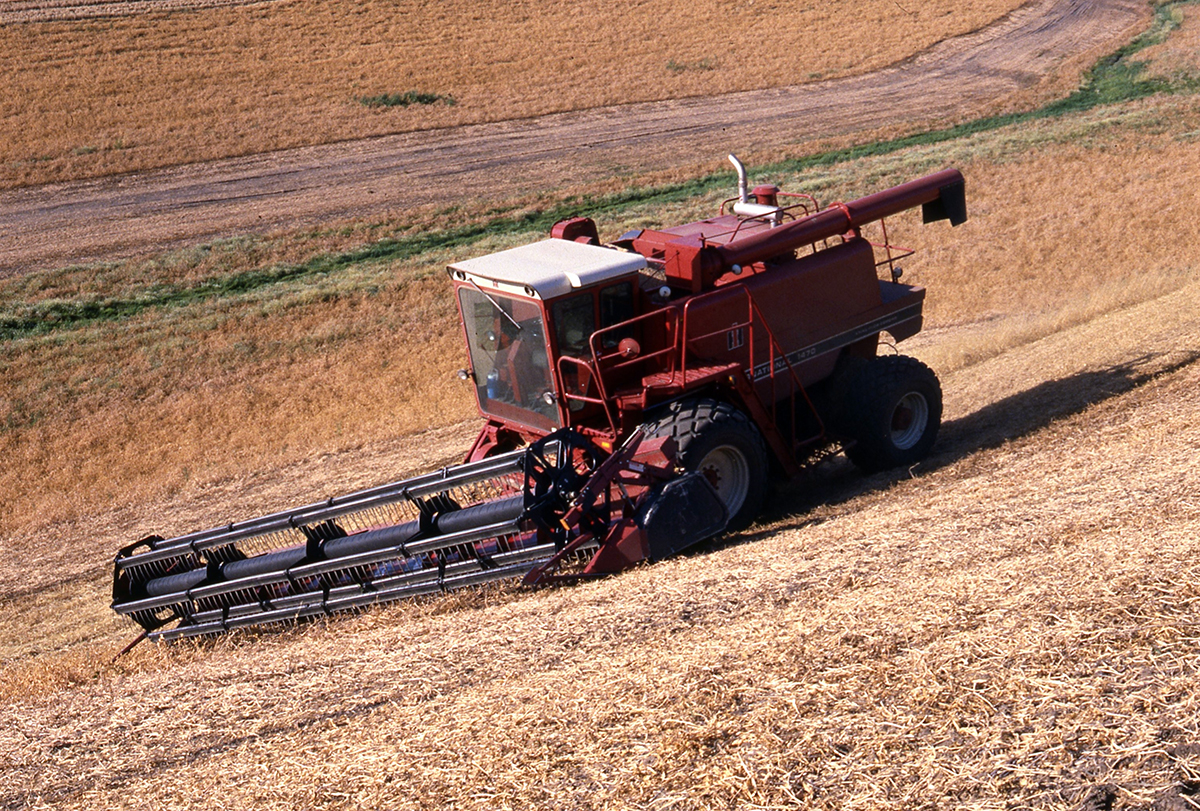
Two-Way vs. Four-Way Leveling
One very real problem in laying out the new machine was the two-way vs four-way leveling argument (maybe our sheet of paper was not so clean after all). We had certain trade areas that depended on the IH four-way leveling machine, and the competition just couldn't get up the steepest hills. We were convinced we could save grain up those steep hills without leveling fore and aft, but we had to get up them. Of course, we intended that only hydrostatic propulsion was suitable, so it naturally evolved (hindsight) that if we could hydraulically drive the rear wheels we could get up those steep hills. This would avoid the cost and "spindleness" of the four-way leveling (I am not sure which would cost the most, four-way leveling or four-wheel drive) so it was agreed all machines would have four-wheel drive. Design criteria were set up, and layout work was started to meet that demand. The criteria included sideslope leveling of 44-49%, the theoretical hill climbing ability was 36%, and the forward tipping slope with full grain tank was 70%. The design actually achieved a sideslope leveling capability of 48%.
Looking for Business Partners in the Northwest
We soon realized that the really large machine that would evolve from our criteria was going to be almost impossible to transport from East Moline to the primary trade area, the Pacific Northwest. So we began looking for someone out in Washington, Oregon, or Idaho that could take a standard 1460 and convert it to a hillside machine. I, among others, traveled extensively in the area, looking for a suitable manufacturer. The most favorable seemed to be Love Company at Garfield, Washington. John Love was primarily involved in the Love pickup reel and the flexible floating cutter bar, both sold nationally. His company also made a bean pickup unit sold locally and some rather mundane rod weeders etc. Moreover he was interested. However we were worried, it looked like we might be shoving an elephant at him that his organization just couldn't handle.
At about this time, somebody, and I sure don't remember who, suggested RAHCO at Spokane. We investigated RAHCO and found them to be a very interesting organization. The name came from no other than Raymond A. Hanson, the inventor of the self-leveling control system. The RAHCO organization, managed by Raymond's three sons was expert in slip-form concrete laying equipment, used primarily in large irrigation canals and pipelines then being built throughout the world. They had bought an old WW-2 aluminum or magnesium producing plant just outside of Spokane, which had become their worldwide operations center. Raymond was semi-retired, spending most of his time sort of playing while still keeping a hand on the boys.
Of course, before IH could seriously discuss a possible joint venture with RAHCO, our legal and business people had to investigate the most intimate details of their financial operations, but eventually all agreed we could consider doing business with these Northwestern mavericks. At the time, they were busy working on one option for hiding and activating the nuclear bomb equipped MX missile. Their proposal was to dig a series of very big trenches in a large area of the Southwest, pouring big, like 15 feet diameter concrete tubes in the trenches, and backfilling the trenches. Then the MX missiles would be randomly located on tracks in the tubes, only the military would know where, thus supposedly immune from enemy atomic attack. At the appropriate time, the MX carrier would use its powerful hydraulic system to burst through the tube and the earth so the MX could blast upward to retaliate. Fantastic and futuristic? They were actually building a system and testing it right in their backyard. We understood it was later shipped somewhere to the Southwest desert, and that a short sample section installed but then mothballed behind a steel fence. I wonder if it is still there.
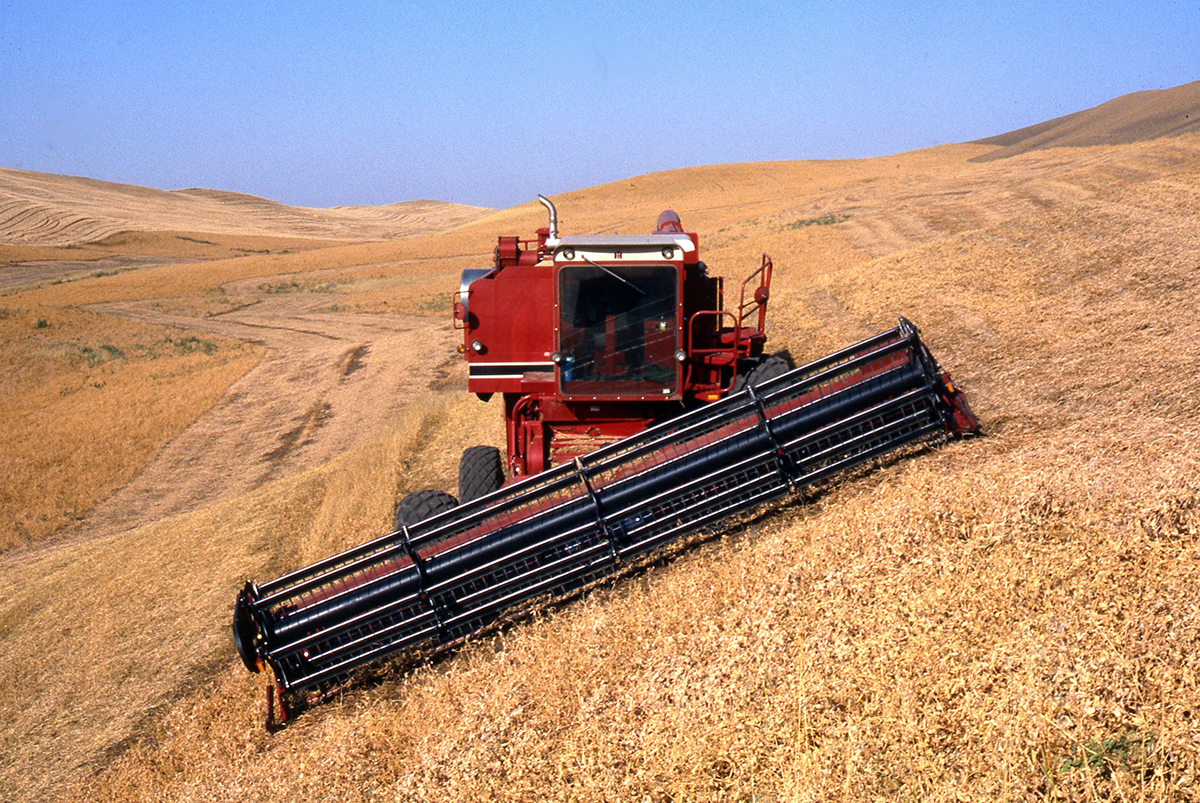
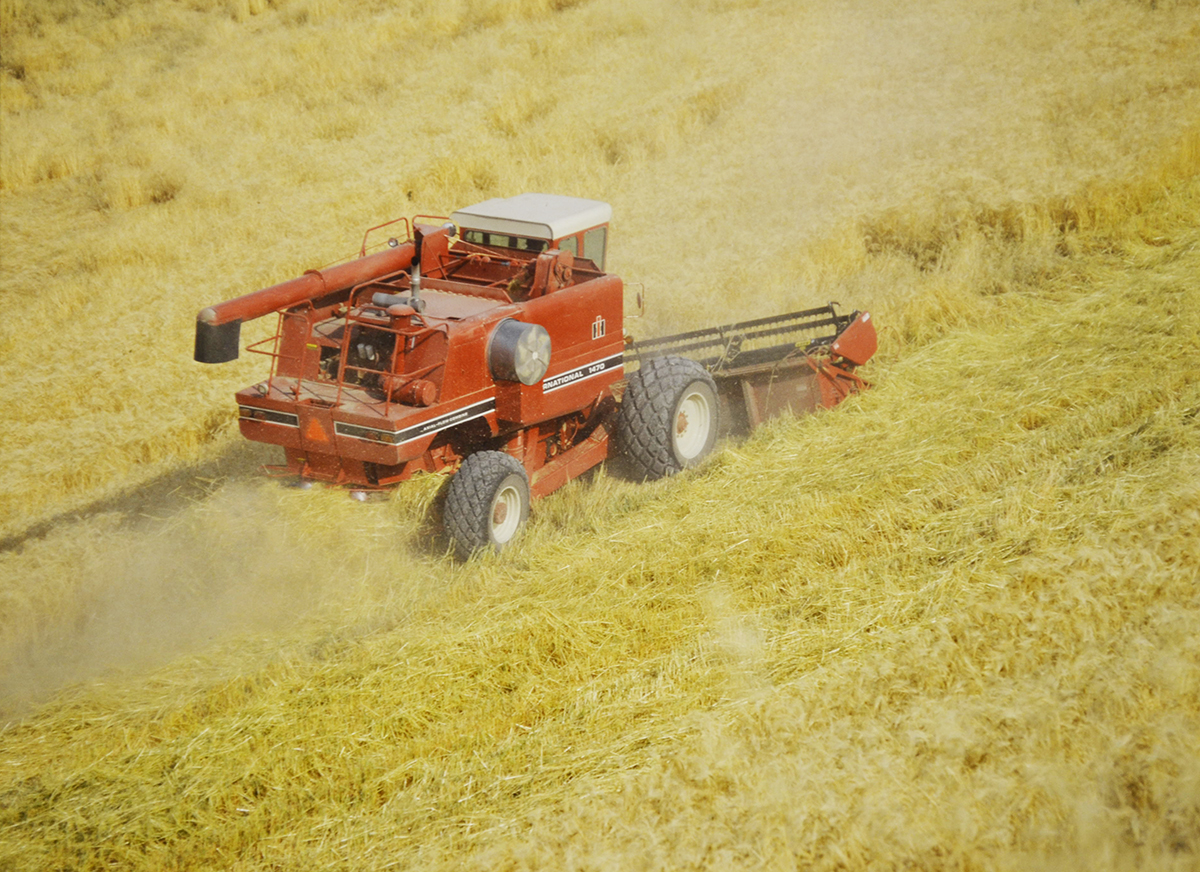
Development Concerns
The concern we immediately saw was that most of their production was one or two of a kind, they didn't worry about mass production, parts interchangeability, and all those things that were vital to us. However they had a good engineering department, and such important things as an established purchasing agent and a good accounting system, and they certainly had the manufacturing space in those big old aluminum production buildings. With all this, we finally signed what we thought was to be a "turn key" deal with them—they would receive a special built 1460 and engineer and build and assemble all the parts necessary to complete the hillside machine.
They hired a project manager, one Guy Swanson who was an Agricultural Engineer with considerable experience in the hillside country. Unfortunately, Guy had little experience in manufacturing and was treated as sort of an outcast by both the RAHCO and the IH people. There were times when I didn't envy him his job. We had set up the criteria, had lots of specifics in the contract, and expected things would go smoothly. But that was not to be the case. Pickett worked with them regularly during their engineering phase, sometimes spending two or three weeks at a time up there. The more he worked with them, the more discouraged he became. They just couldn't seem to get away from their "build it extra stout and don't worry about the cost" theory. I found I was up there several times to try to negotiate a peace between IH requirements and RAHCO objectives. When RAHCO people thanked me for my decisions I knew Leroy was not going to be happy, and visa-versa.
Preproduction Tests
Our test department rightly insisted the test machine be checked for structural weakness.
One trip while I was up there, Jim Lucas was applying stress-coat (brittle lacquer some called it) to a large number of areas he by judgment deemed might be critical. Conditions there were not favorable to stress-coat, but as I remember it he had a new formula that could be applied and cured at ambient temperatures. Then they took the machine out on representative hillside applications, brought it back and analyzed the stress crackage patterns—a standard procedure for them but Greek to the rest of us.
In 1979 we had RAHCO build five preproduction machines, which we and marketing placed throughout the hillside area (placed, not sold). Four of them remained in the Northwest, but the fifth, at marketing's insistence, had to go down to Paso Robles, California. There was a small pocket of hillside market down there, not really appropriate for one of the five. The machine had to be partially disassembled and then shipped as a special wide-load truck shipment. Because it was so far from the rest of the activity, it never got good service and was a detriment to the sales area.
Sometimes we are slow to learn, or maybe reluctant to vigorously resist sales "demands," particularly those made by the big California dealers.
Announcing the Model
For some reason that now escapes me (and seems a year premature} on June 19, 1979, we had a big product announcement at the convention center at Spokane introducing the 1470 Hillside Combine to IH marketing people and dealers. We had a machine there, a big slide introduction to the dealers, and I specifically remember Tom St John got stuck with announcing the list price—$115,000 (later increased to $121,688)—far and away the highest price ever asked for a combine (by comparison the 1460 Corn Special with six row corn head was $90,000 and the 453 in 1976 was $50,782, 1977 dollars). There was a gasp from the dealers but by the time the day was over they were reasonably receptive. In D & T 310, 10-20-76 we had projected a list price of $68,423 (1977 dollars) for a two-way leveling, two-wheel drive 1460 Axial-Flow Hillside Combine. Obviously, we had raised our sights—and our costs—considerably.
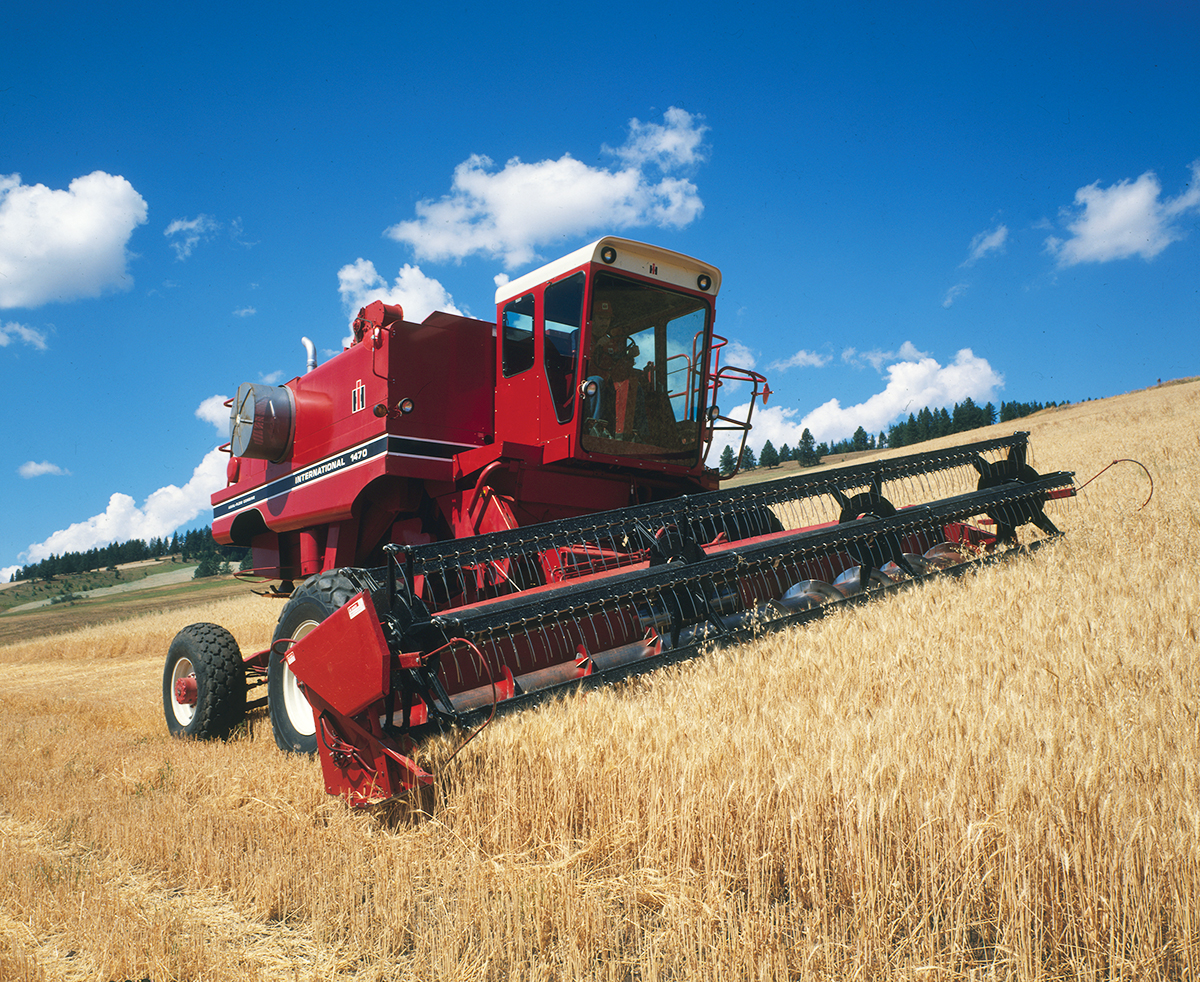
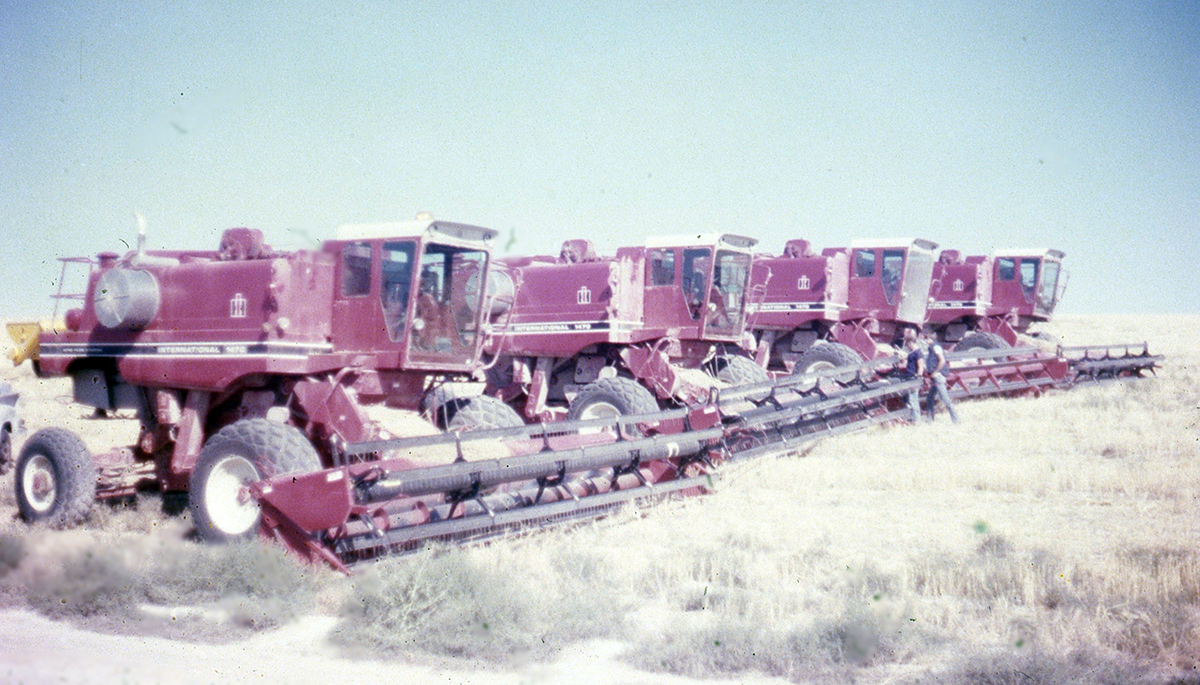
Much-Needed Improvements
By August of 1979, quite a number of machine areas had surfaced that demanded improvement. Also, the marginal "producibility-reliability" of the RAHCO drawings was becoming evident. We had both Leroy Pickett and Rich McMillen, along with three or four other of our own Product and Test Engineers up there working on solutions. In addition we had three or four engineers back at East Moline working on the design and drawings.
Leroy wanted to bring all the drawings back to East Moline and have our own engineers go over the whole design and upgrade the drawings to our standards. I did not agree with this, not that it was not the best program for the hillside but that it would have been a major disruption to all the rest of our programs. Rich finally worked out a compromise where East Moline Engineers went over a lot of the really critical areas and worked with RAHCO engineers on the rest of the design. Right in the middle of this, Gene Krukow, Norm Stroup and Dick Staiert were having a field day with all the real "gut issues": the hydraulics and electronics involved. They worked well with the rest of the group and the challenge of this project was what they had dreamed of for years. In many ways the ultimate success of the program was due to their aggressive understanding and solution of complex hydraulic, hydrostatic propulsion and electronic control challenges, together with Leroy Pickett's dogged determination to have a machine that was right and Jim Lucas' continual evaluation of the product to see that it was right. It was an excellent team effort.
Into Production
By early 1980, IH and RAHCO worked out the problems both in design and with the contract, and went into production. Considering the tremendous internal problems that had to be resolved, the resulting product was a very good professional representation, a product both IH and RAHCO were proud of. What had started out to be a "turn key" product where RAHCO was to do all the "hill siding" had gradually evolved into IH both paying RAHCO for their engineering effort and investing considerable of our own engineering manpower. The project ended up costing our engineering department just over $1,000,000: double our original estimate. But, very important, IH got the manufacture and distribution problems resolved. We also got into production one year earlier than our 1976 projections (1980 vs. 1981).
We never did go back and try to develop a "sidehill" version of the Axial-Flow to match the JO Sidehill 6600. Deere Sidehill 6600 sales were never spectacular, but they did justify the one model. In 1976 they sold 654 units (Macmillen and Harrington, John Deere Tractors and Equipment, Vol. 2) which is estimated at a little over 10% of their 6600 sales. If we had proceeded, it is doubtful if we could have gained much net sales. Incidentally, as I understand it Deere later went to RAHCO to have them produce the next generation JD hillside model. By that time, I was retired and not worrying about who owned tooling, engineering and all the ramifications. As far as I know the arrangement is still in effect.
Pickett, Stroup and Lucas presented a paper at the 1980 Winter Meeting, American Society of Agricultural Engineers 5, and later in October 1981, Norm Stroup and Gene Krukow presented a paper describing the hydraulic system at the National Conference on Fluid Power. IH Combine Engineers were again showing the professional societies that they were pushing the frontier in engineering farm machinery.
Production Figures
We here only have production figures for 1980 and 81. There are two or three sources of figures, which for a change do agree. It appears that in 1980 we shipped 130 machines to RAHCO for conversion and in 1981 we sent 170 units out to Spokane or 300 in the two years (plus the five reconditioned pre-production machines). Another chart shows retail sales of 102 in 1980, 145 in 81 with inventory of 58 at end of 81 or 305 total accounted for. The annual total market for hillside combines at that time was probably 300–500 machines (in 1976 Deere sold about 260 6602 machines, probably their best year). We had been selling 130-160 of the 453's in the mid and late seventies. Of course one irony was that in presenting a substantially larger combine we were cutting the market potential in unit volume.
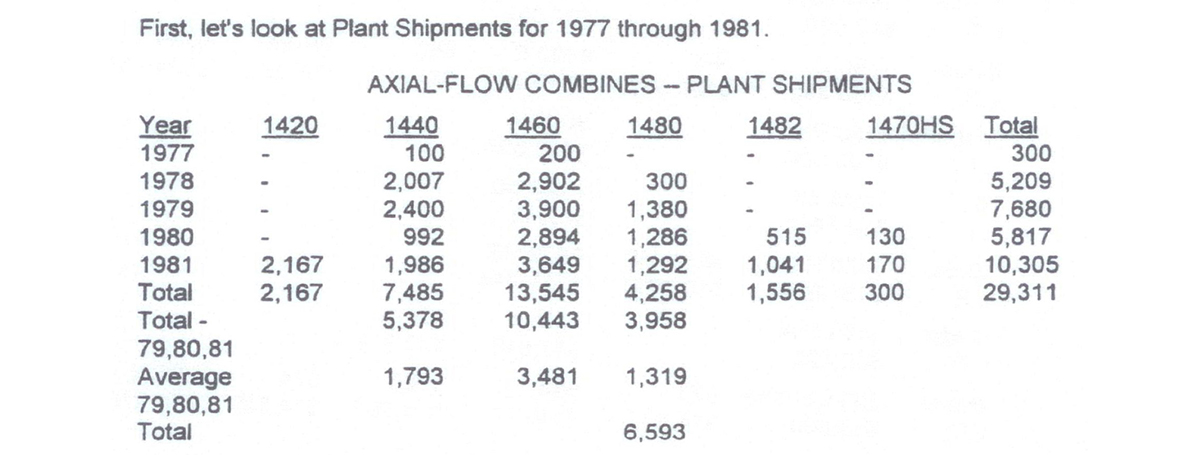
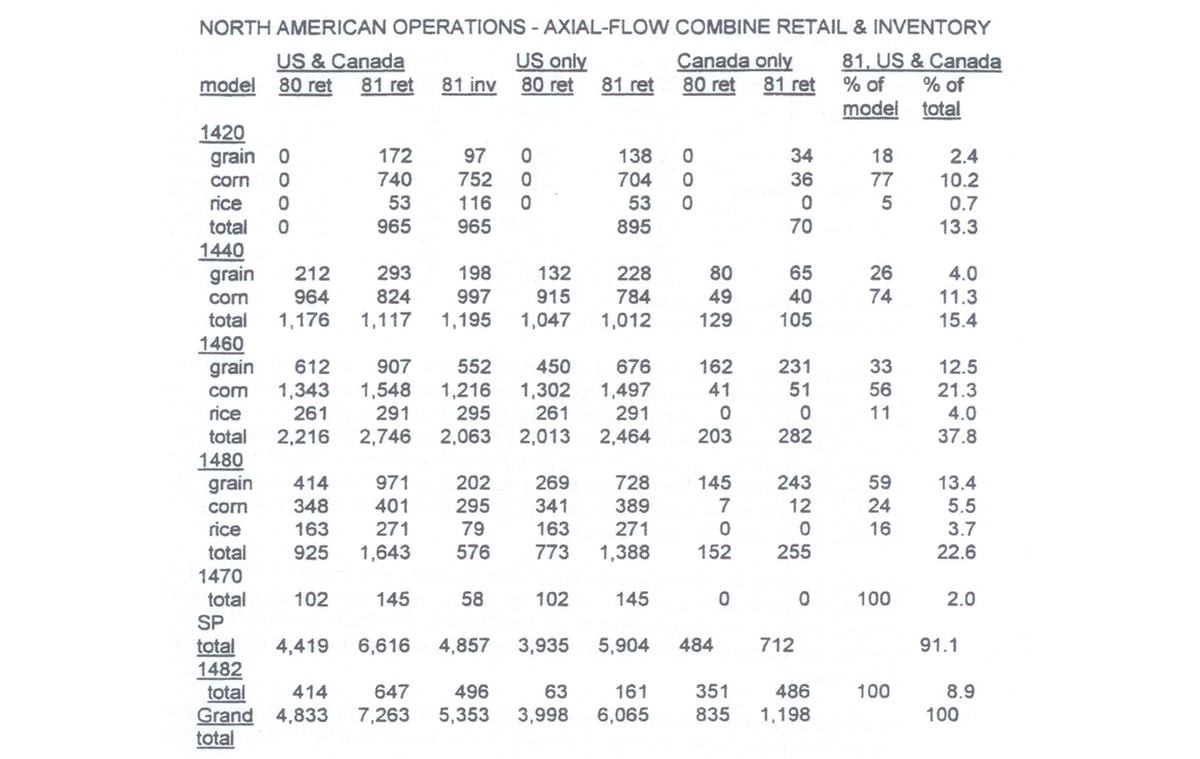
At a retirement celebration at East Moline in June, 1982, Bev and I were presented with a beautiful framed photograph of four 1470 combines harvesting double windrows of Kentucky Blue Grass just Southeast of Spokane. On the back is an explanation. "A family of four brothers owned eight John Deere's. They traded them in for four IH combines. It is well known that one 1470 will do the work of two John Deere's," -- Camiel Beert.
This whole hillside endeavor is a typical example of IH efforts to fill the "niche markets" to obtain overall coverage throughout the country and to provide local IH dealers in each area a full line of products for their area needs.
Find more engineering and development narratives from Don Murray's experience leading the Axial-Flow combine project in Red Combines 1915–2015.