Creating the Magnum Tractor
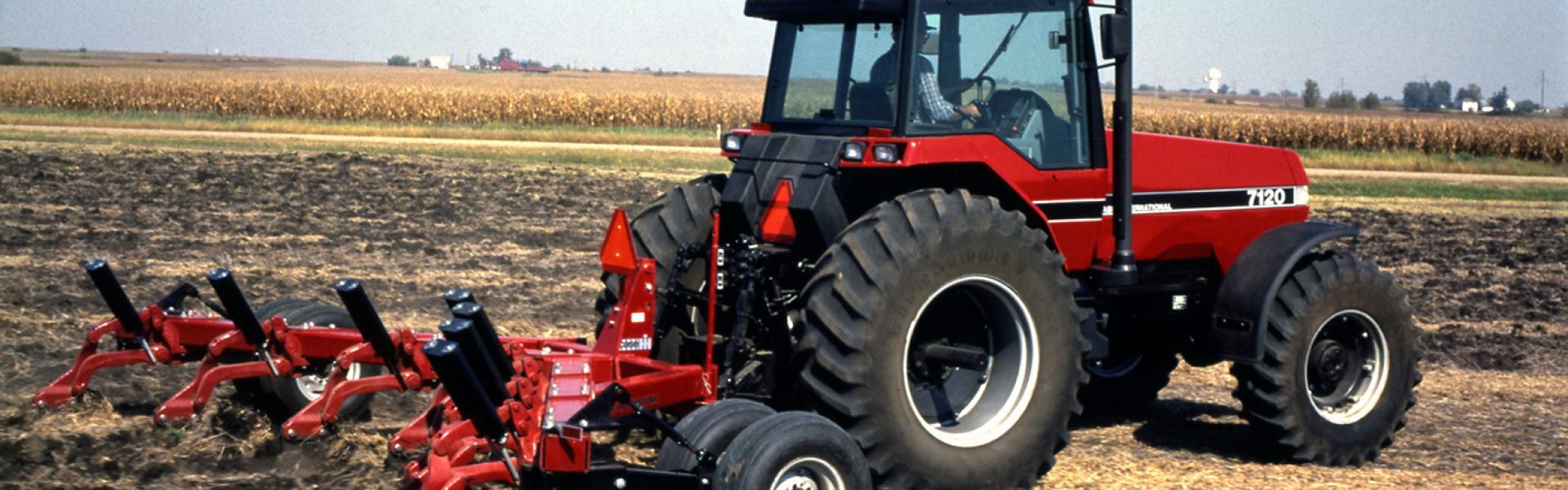
The key to creating the machine that would become the Magnum was proper assembly of the parts that the company already had in place. Harvester had a good engine, but Cummins and Case had started a joint venture in 1980, the Consolidated Diesel Company (CDC), to build clean-burning diesel engines for Case machinery and to sell as OEM units. The CDC engines were high-quality units that came on line in 1983, so the decision was made to use them rather than the Harvester powerplant.
Early Magnum concept art. Gregg Montgomery Collection
Also, Case had a good test program and the director impressed Kahle. “I put the guy in charge of their tests in charge of the new organization’s test activity,” he said.
According to Kahle, the engine and the under-hood exhaust routing were among the few existing Case tractor systems used to create the first Magnum. “We didn’t use much of anything from the Case tractors,” he said. “The technology simply wasn’t up to the level we had at Harvester.”
This early rendition of the Magnum was built in 1987. Gregg Montgomery collection
The frame for the Magnum started out as a Harvester design, but it changed so much that Kahle said you would never recognize it as such. The frame wasn’t the only component to evolve in the two years during which the Magnum tractor was developed.
The Harvester engineers had wanted to build a new cab for a while, but lacked the funds.
Concept art of the Magnum Tractor. Gregg Montgomery Collection
The money from Ketelsen changed that. The new cab would have only one door rather than two, and the team opted to avoid going fully electronic as the componentry available at the time wasn’t reliable enough. The console was all-new, as was a system that warned the operator of dangerous conditions. There was also a limp-home mode that allowed the tractor to be driven (slowly) home from the fields in case of failure.
Fuel tanks were molded and placed under the operator stations. The new tractor held more than 75 gallons of fuel, and an optional tank could hold 95 gallons—roughly double the capacity of competitive tractors.
The transmission was another hotly debated topic. Harvester had a synchronized transmission that had been in production since 1981. That it would be converted to a full power-shift transmission there was no question. But Deere offered several transmission options. Many believed Case IH should do the same.
The transmission in the fourth-generation Magnum had deep roots with the power-shift unit developed for the first-generation units in the 1990s. The early transmission was smartly engineered and rigorously tested. CNH Global
“Deere had a mechanical transmission and then they had a full power-shift transmission, and there was a big debate whether we should have two different transmissions or not. In the end we didn’t have the money, I don’t think, or the horsepower or people to do it, so we went with just the one full power-shift transmission,” Steve Warner said. “[We] were coming [out] with a brand-new tractor with only one transmission option . . . and Deere had at least two. So there was a lot of concern and a lot of questioning and a lot of scuttlebutt around Burr Ridge about whether that was the right decision, would we be successful or not.”
Once the decision was made to go with one transmission, the problem became transforming the 88 Series synchro-shift transmission into a full power-shift.
“That transmission was the key to the whole tractor,” Kahle said. “It’s the only one to my knowledge, even to this day, that the final speed [adjustment] occurs in a mid-mounted clutch.”
The key to a power-shift transmission is allowing the operator to shift smoothly on the fly. The technology behind the development is complex, particularly considering the electronics that were reliable enough to consider at that time. The control of the shift would have to be done mechanically.
In essence, the Case IH engineering team created a master clutch that was mid-mounted. The clutch engaged automatically when the operator shifted, and the operation was controlled by a rotary valve.
Ben McCash was the team leader for the transmission development. He described designing that power-shift transmission—and specifically the rotary valve—as one of the most significant engineering challenges of his career. He recalls a team of 14 engineers assigned to the transmission project, plus some technicians who provided support.
“The Magnum was a challenge. We started out on that trying to come up with a reasonable way to shift all the way through to create a power-shift transmission that gave us shifts that were not a shock to the operator,” McCash said. “We were doing this with a mechanically controlled valve. Because at this point in time, we still did not have good electronic capability, so we took a control valve that had three spools in it that were controlling the different clutches in the transmission.”
The front section of the transmission was a two-speed unit, followed by two separate three-speed units.
The Magnum cab was a revised version of a cab that IH had on the drawing boards in the late 1980s. This is an early interior mockup. Gregg Montgomery collection
“This was all controlled in this valve by three spools that controlled these three different sections of the transmission, and they were mechanically operated,” McCash said. “So what we ended up doing was building, taking a cam that operated these all simultaneously, and we had to then rotate that cam, each stop on the cam would be another gear in the transmission. Developing that valve turned out to be probably the most difficult thing in the Magnum transmission. I had one development engineer in the test department working full-time for about three years at valves.”
According to McCash, 14 to 18 different versions of the valve were developed before it operated correctly. Kahle estimates there were 25 to 27 patents developed for the Magnum transmission alone.
Each of the new iterations was put through an exhaustive test process.
The Magnum’s new cab offered terrific visibility, and the switch to a single door allowed more ergonomic placement of the controls. Gregg Montgomery collection
“We had two transmissions in the laboratory that were running almost constantly, testing out the transmissions with these control valves,” McCash said. “We had done more testing on that transmission than on any transmission before or since. I actually tabulated the number of test hours that we ran on the different units we had. We had over 20 different transmission test units, and they ran a total of 86,000 hours in the laboratory.”
An early production version of the Magnum 7120. Gregg Montgomery collection
The test program was more thorough than what had been done in the past. “We had done some testing after the design was developed on the 50 series. We did some in the lab, but most of the 50 series testing was done in the field. When we first went into production on the 50 series there was a problem found with the differential, and we went into a very extensive laboratory test program to develop a solution to that problem. And that program kind of became the prototype for what we did then on the Magnum program. We put together a number of test units, we had people who followed them 24 hours a day, 7 days a week and who were very rapid in turning things around and putting new parts in, checking out new designs and moving on to the next one.”
To find out the rest of the incredible story of International Harvester, get your copy of Red Tractors 1958-2013 here!
Previous Excerpt - Next Excerpt